Safety is more than a checklist; it’s a mindset.
As industries evolve, so must our approach to creating safer work environments. Global Industrial is committed to helping businesses across sectors stay ahead of safety regulations and trends. In 2024, the Occupational Safety and Health Administration (OSHA) continued to focus on reducing workplace injuries and fatalities by highlighting the most common safety violations.
But (and this is a big consideration), OSHA's guidelines are only part of the bigger picture. Businesses must also consider emerging safety trends, from heat stress regulations to the changing dynamics of remote and on-the-go workforces. We’ll get into that in a moment, but first, let’s look at the 2024 offenders.
Here’s a comprehensive breakdown of OSHA’s top 10 safety violations for 2024, followed by our opinion on broader trends that we believe are reshaping workplace safety.
OSHA’s Top 10 Safety Violations for 2024
Each year, OSHA releases a list of the top 10 most frequently cited workplace safety violations. These citations often point to persistent safety gaps across industries and provide a roadmap for areas that need heightened attention. And, once again, the top 10 list isn’t very different at all from previous years. It leads to a big question: what good is the list if it isn’t changing workplace health and safety procedures? For 2024, the OSHA safety violations are as follows:
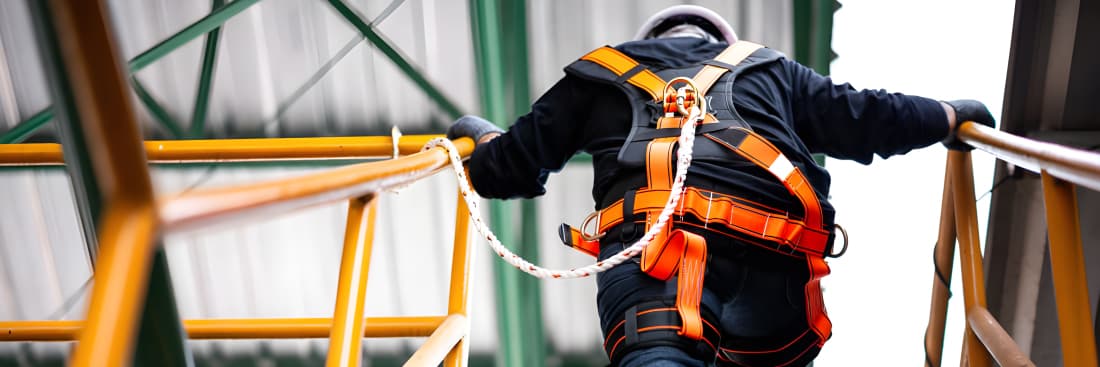
CATEGORY | VIOLATIONS IN 2024 | DESCRIPTION | |
---|---|---|---|
1. | Fall Protection - General Requirements (1926.501): | 6,307 violations | Falls continue to be the leading cause of death in construction, making fall protection a perennial concern. The general requirements mandate that workers must be protected from falls when working at heights of six feet or more. The OSHA fall protection standard is, once again, a major issue that’s being ignored. |
2. | Hazard Communication (1910.1200): | 2,888 violations | Proper labeling and handling of hazardous chemicals are critical for workplace safety. Violations often occur when employers fail to communicate the risks associated with chemicals, leading to potential exposures and health risks. Hazard communication standard continues to be a top concern. |
3. | Ladders (1926.1053): | 2,573 violations | Ladders are essential in many industries, yet improper use or faulty ladders contribute to thousands of injuries each year. OSHA's ladder safety standards focus on proper ladder use, inspection, and maintenance. |
4. | Respiratory Protection (1910.134): | 2,470 violations | Respiratory hazards can be life-threatening, especially in industries involving dust, fumes, and vapors. Employers are required to provide adequate respiratory protection and ensure employees are trained on proper use. |
5. | Lockout/Tagout (1910.147): | 2,443 violations | This standard prevents the unexpected release of hazardous energy during machine servicing. Lockout/tagout violations remain a serious issue, especially in manufacturing environments where machinery is frequently serviced or maintained. |
6. | Powered Industrial Trucks (1910.178): | 2,248 violations | Forklifts and other powered industrial trucks are common in warehouses and factories, but improper training, maintenance, or operation can lead to catastrophic accidents. OSHA's standard emphasizes the safe operation and maintenance of these vehicles. |
7. | Fall Protection – Training Requirements (1926.503): | 2,050 violations | Proper training in fall protection is essential for worker safety. This standard ensures that employers provide adequate training to employees on fall prevention and protection measures. |
8. | Scaffolding (1926.451): | 1,873 violations | Scaffold safety violations occur when scaffolding is improperly erected or used, leading to falls or collapses. OSHA's standards aim to ensure that scaffolding is safely constructed and maintained. |
9. | Personal Protective & Lifesaving Equipment – Eye and Face Protection (1926.102): | 1,814 violations | Eye and face injuries can be prevented with the proper use of PPE. Violations often occur when employers fail to provide or ensure the use of adequate protective gear. |
10. | Machine Guarding (1910.212): | 1,541 violations | Machine guarding violations occur when machines are not properly equipped with safety guards, exposing workers to moving parts that can cause severe injuries. This is a warehouse safety issue that continues to be in the top 10 OSHA list. |
So, What’s New in 2024/2025? Let’s Look at Emerging OSHA Trends.
Beyond addressing common OSHA safety violations, OSHA has rolled out new initiatives and rules aimed at tackling emerging hazards. Here are some noteworthy developments:
1. Annual Safety Reporting for High-Hazard Industries
Employers in certain high-hazard industries with 100 or more employees must electronically submit detailed reports on workplace injuries and illnesses. This new requirement aims to increase transparency and allow OSHA to gather more nuanced data on safety risks.
Global Industrial’s Stance: While some businesses view this as an administrative burden, we see it as an opportunity. By gathering more detailed industrial safety data, companies can identify trends, optimize their safety programs, and potentially reduce long-term injury-related costs.
2. Heat Stress Regulations on the Horizon
OSHA is poised to introduce its first-ever national rule addressing heat stress, a growing concern as climate change leads to more extreme temperatures. This regulation will likely require employers to implement robust heat illness prevention measures, especially for outdoor and high-heat indoor environments. Employers should anticipate these changes and proactively implement heat safety protocols, such as hydration programs, rest breaks, and environmental controls.
Global Industrial’s Stance: We fully support a heightened focus on heat safety. With a range of products from cooling gear to temperature control systems, we’re ready to help businesses protect their employees from heat-related illnesses.
3. Warehouse and Distribution Center Emphasis Program
Recognizing the rapid growth of the warehousing industry, OSHA has launched a three-year National Emphasis Program (NEP) aimed at improving safety in warehouse and distribution centers. This initiative focuses on reducing hazards such as struck-by incidents, caught-in-between accidents, slips, and ergonomic issues, all of which are common in high-activity warehouse settings. Given the rise of e-commerce, this NEP comes at a critical time.
Global Industrial’s Stance: We support OSHA’s efforts to make warehouses safer. From protective barriers and bollards to signage and personal protective equipment (PPE), we provide a range of products designed to prevent common warehouse injuries.
4. New PPE Standards for Construction
OSHA has proposed a revision to its PPE standards in the construction industry, requiring that all protective gear fits properly. Poorly fitting PPE can render safety equipment ineffective and put workers at risk. Ensuring that workers of all sizes have access to well-fitting PPE is a simple yet crucial step in improving workplace safety.
Global Industrial’s Stance: Employers should offer a range of PPE sizes to ensure proper fit. We supply a variety of safety gear, including customizable options to meet the specific needs of diverse workforces.
Looking Beyond OSHA Safety Violations: New Safety Considerations To Explore…
While OSHA’s regulations provide a critical baseline for workplace safety, today’s businesses must also look beyond these guidelines to address emerging risks and challenges in a rapidly changing world.
Safety BEYOND the Workplace
As remote work, off-site jobs, and mobile workforces become more common, companies need to expand their safety programs to cover environments beyond the traditional workplace. Road workers, construction crews, delivery drivers, and emergency personnel often work in changing and unpredictable conditions, posing unique safety challenges.
Global Industrial’s Stance: Safety planning and prevention must account for risks that employees face while working off-site. Whether it’s on the road, at a vendor’s facility, or at a remote location, businesses need to ensure their employees have the safety equipment and training necessary to stay protected.
Extreme Weather Preparedness
With climate change leading to more extreme weather events—such as wildfires, floods, and extreme heat or cold—companies must be prepared for the impacts of unpredictable conditions. Power outages, disrupted supply chains, and increased worker hazards during extreme weather are just a few of the challenges businesses face.
Global Industrial’s Stance: We offer a range of seasonal safety products to help businesses prepare for and respond to extreme weather events. From emergency lighting to portable heaters and cooling units, we provide solutions to keep operations running and employees safe in adverse conditions.
The Bigger Picture: Making Safety a Core Value
At Global Industrial, we believe that safety should be more than just compliance with OSHA standards—it should be a core value embedded into every facet of business operations. By taking a proactive approach to safety, companies can not only avoid costly fines and injuries but also foster a culture of safety that drives efficiency, productivity, and employee well-being.
Here are three ways businesses can make safety a cornerstone of their operations:
- Invest in Ongoing Training: Safety training should be a continuous process, not a one-time event. Regular training sessions help ensure that employees stay up-to-date on the latest safety protocols and best practices.
- Leverage Data for Decision-Making: With new OSHA reporting requirements and the availability of advanced analytics tools, companies can gather valuable data on workplace incidents and use it to make informed decisions about where to focus safety efforts.
- Promote a Safety-First Culture: Leadership teams should model a commitment to safety by making it a top priority in all business decisions. Encouraging employees to speak up about potential hazards and rewarding safe practices can go a long way in fostering a safety-first culture.
As industries continue to evolve, so do the risks that workers face on the job. While OSHA’s Top 10 safety violations provide a useful snapshot of the most pressing safety issues, businesses must also stay ahead of new developments and trends that impact workplace safety. By investing in the right safety products, staying informed on regulatory changes, and fostering a culture of safety, businesses can protect their workers and create a more resilient operation.
Global Industrial is proud to be your partner in safety, offering a wide range of solutions to meet the pressing needs of today’s workplaces. Whether you’re looking to prevent falls, improve heat safety, or prepare for extreme weather, we’re here to provide the tools and expertise you need to keep your workforce safe. Contact us any time, we’ll be happy to provide the best guidance available.
The information contained in this article is for informational, educational, and promotional purposes only and is based on information available as of the initial date of publication. It is the reader’s responsibility to ensure compliance with all applicable laws, rules, codes and regulations. If there is any question or doubt in regard to any element contained in this article, please consult a licensed professional. Under no circumstances will Global Industrial® be liable for any loss or damage caused by your reliance on this article.