OSHA (the Occupational Safety and Health Administration), plays a significant role in maintaining workplace safety. We rely on the organization for upholding safety standards, alerting us to new and/or rising dangers, and to penalize those who ignore (either accidently or on purpose) the regulations.
With the release of the 2023 hazard violations list, we have to ask some tough questions if we want to use this information to improve safety in the workplace. First and foremost, what can be done to reduce the reoccurring violations that occur year after year?
Around the end of October, OSHA historically releases the top ten safety violations discovered at job sites in that calendar year. This usually comes from two sources; on-site inspections, or employees reporting unsafe working conditions. We have seen the same violations year in, year out, with OSHA Fall Protection (General Requirements) topping the list in 2023 for the 13th year in a row. If your job involves working at heights, take note.
The National Safety Council (NSC) seems to be aware of the issue. “Although incredible advancements are made in safety each year, we continue to see many of the same types of violations appear on OSHA’s Top 10 list,” said Lorraine Martin, NSC president and CEO. “As a safety community, we must come together to acknowledge these persistent trends and identify solutions to better protect workers.”
Lorraine Martin’s statement is accurate. Despite many advances in safety equipment and procedures, and strenuous efforts by OSHA to enforce the regulations, violations continue to increase.
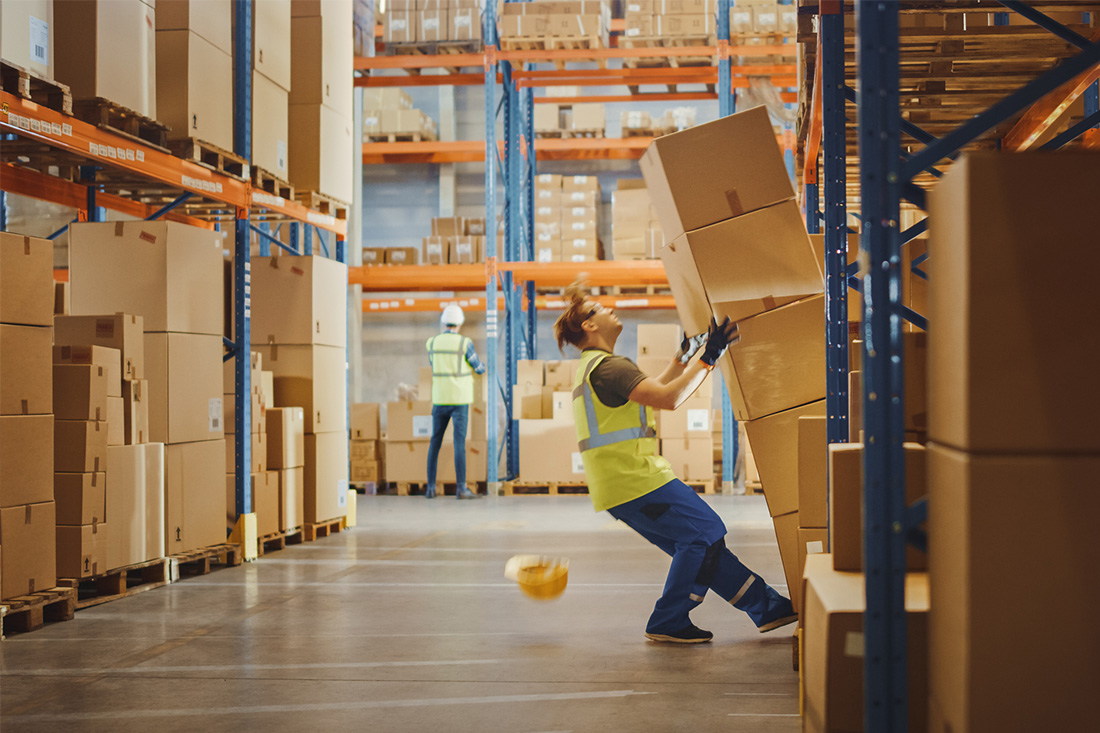
Indeed, some 29,747 OSHA safety violations make up the total top 10 list for the 2023 financial year, up from 22,123 in 2022; an increase of 34.5% in just one year!
This trend prompts two critical questions: why is it occurring, and what can be done to address it? Collectively we have to acknowledge that we can all do more to create a safer workplace. We know that there is not a significant increase in the number of employees to account for the increase in violations. In fact, the construction industry for example, employed some 8.03M people in 2023, up slightly from 7.84M in 2022. The 3% increase in construction employment does not correlate to the year-over-year increase of 34.5% of violations, something else is driving this increase.
With all the advances in safety, coupled with the latest tech, software, and knowledge, these types of OSHA violations should be going down every year, not rising. Which leads to a important question;
What can be learned from the OSHA Top 10?
Let’s start by looking at the numbers for 2023, with a brief look back at the previous two years:
1: OSHA Fall Protection – General Requirements (1926.501): 7,271 violations
(Also #1 in 2022 - 5,260 violations; And #1 2021 - 5,271 violations)
2: Hazard Communication (1910.1200): 3,213 violations
(Also #2 in 2022 - 2,424 violations; Up three places from #5 in 2021 - 1,947 violations)
3: Ladders (1926.1053): 2,978
(Up one place from #4 in 2022 - 2,143 violations; Steady at #3 in 2021 - 2,026 violations)
4: Scaffolding (1926.451): 2,859
(Up one place from #5 in 2022 - 2,1058 violations; Steady at #5 in 2021 - 1,948 violations)
5: Powered Industrial Trucks (1910.178): 2,561
(Up two places from #7 in 2022 - 1,749 violations; Up five places from#9 in 2021 - 1,420 violations)
6: Lockout/Tagout (1910.147): 2,554
(Also #6 in 2022 - 1,997 violation; Steady at #6 in 2021 - 1,698 violations)
7: Respiratory Protection (1910.134): 2,481
(Down four places from #3 in 2022 - 2,185 violations; Down five places from #2 in 2021 - 2,527 violations)
8: OSHA Fall Protection – Training Requirements (1926.503): 2,112
(Also #8 in 2022 - 1,556 violations reported; Down one place from #7 in 2021 - 1,666 violations)
9: Personal Protective & Lifesaving Equipment – Eye & Face Protection (1926.102): 2,074
(Also #9 in 2022 - 1,401 violations reported; Down one place from #8 in 2021 - 1,452 violations)
10: Machine Guarding (1910.212): 1,644
(Also #10 in 2022 - 1,370 violations; Steady at #10 in 2021 - 1,113 violations)
That despite that the same ten standards are being repeated annually (albeit in a slightly different order), the number of violations is, for the most part, rising with each passing year. And of particular interest is the rise in fall protection violations, which not only keeps the top spot annually, but is increasing by substantial numbers. We once again need to ask…why?
So…Why Are OSHA Violations Rising When They Should be Falling?
Well, one reason could be the way OSHA penalizes offenders.
Type of Violation | Penalty Minimum | Penalty Maximum |
---|---|---|
Serious | $1,116 per violation | $15,625 per violation |
Other-Than-Serious | $0 per violation | $15,625 per violation |
Willful or Repeated | $11,162* per violation | $156,259 per violation |
Posting Requirements | $0 per violation | $15,625 per violation |
Failure to Abate | N/A | $15,625 per day unabated beyond the abatement date [generally limited to 30 days maximum] |
For a repeated other-than-serious violation that otherwise would have no initial penalty, a GBP penalty of $446 shall be proposed for the first repeated violation, $1,116 for the second violation, and $2,232 for a third repetition.
As you can see, serious violations have a maximum penalty of $15,625 per violation. And the fines are raised for willful or repeated offenders, with maximum penalties of $156,259 per violation. While that is a substantial amount for an independent contractor or mom ‘n’ pop shop, major corporations and conglomerates can absorb these penalties with minimal impact to their overall business. As such, it may make sense to scale penalties proportionately to the size of the business or as a percentage of annual revenues.
At the start of 2023, OSHA announced an expanded penalty policy, with an enforcement policy that can apply “high-gravity serious violations” to falls, machine guarding, respiratory protection, permit required confined spaces, lockout/tagout, and trenching. But again, it seemingly will impact smaller businesses, more so than larger companies with deeper pockets.
Recording of complaints may be another area to examine. OSHA has several ways to record complaints, from on-site inspections and unannounced visits, to whistleblowers who can go online, call, fax, email, send a letter, or even go to an OSHA office in person. Creating a collaborative environment where all parties involved are incentivized to bring attention to issues prior to them becoming violations could proactively reduce more safety risks.
Given all of these factors, OSHA's annual Top 10 may not be identifying some of the best opportunities to improve safety in the workplace. Other KPIs may be more informative in finding actionable insights to improve safety. Perhaps examining the top 5 reasons for violations being overlooked can guide more impactful action. OHS lists the five common reasons for safety violations being overlooked are:
1. Employee burnout
2. Time constraints and tight deadlines
3. Overconfidence among employees
4. Lack of regular training
5. Miscommunication
While the OHS Top 5 is certainly a good start, there are many additional potential causes for the increase in violations, including:
- Uncomfortable and ill-fitting PPE, especially for female workers.
- Poor judgement: “I’m only going up for a minute, I’ll be fine” is a very dangerous way to work.
- Unorganized and outdated equipment. Although something was the top of its class a decade ago, it could be sorely inefficient, or even dangerous, in today’s workplaces.
- Confusing and poorly-worded regulations; if you can’t understand the rules it’s harder to follow them.
- Reassurance from managers and the C-Suite that “everything’s fine, don’t worry, you’re safe,” which is not always the case.
- Not taking OSHA and the penalties seriously. It’s no secret that OSHA is handling more violations with fewer staff, and just like an IRS audit, more employers don’t think it will happen to them.
So, What Can Be Done To Improve Safety?
At Global Industrial, we’re focused on finding solutions. And whether that’s providing the best tools for the job, equipment for your team, or expert advice on a wide variety of trades and industries, we’re in this to make things better.
OSHA continues to make strides in driving greater awareness for workplace safety, and the annual top ten list is a great reminder for all of us to reassess our operational safety risks. But, there are factors we should consider that can improve workplace safety.
For example, OSHA is seemingly understaffed. A 2022 Department of Labor report called “U.S. Department of Labor’s Top Management and Performance Challenges” revealed a considerable staffing shortage. The total number of inspectors fell from 860 in 2014 to an all-time low of 750 in 2021 (this does not include States with OSHA-approved State Plans). And while OSHA’s budget has increased in recent years, its $632 million budget for FY 2023 reflects a $20 million increase from FY 2022; that’s roughly a 3% increase, way under the $90 million that was asked for. We need to pressure our representatives to increase funding and staffing at OSHA.
We should also reconsider the fines themselves. Perhaps OSHA should impose bigger fines and consequences for repeated violations, scaled based on the size of the organization, and encourage business owners to collaborate with their employees to proactively and continually reduce safety risks.
While OSHA is enforcing the penalties it imposes, as an example let’s look at Dollar General being hit with $15.5 million in penalties since 2017. With Dollar general’s profits in the last three years being well over $32 billion, in comparison the $15.5 million in fines is minimal. This appears to be a case of it being cheaper to pay the fines than to put proper safety procedures in place, as was recently mentioned on “Last Week Tonight with John Oliver.” And no doubt many other companies are taking that route.
Since these safety standards and violations are ultimately in place for the health and safety of our fellow workers, and ourselves, we need to do better. This is a conversation that should take place annually with all stake holders empowered to submit solutions for new and innovative ways to improve workplace safety.
Currently OSHA should reconsider their existing penalty policy, and what steps can be taken to curb the violations. Beyond financial penalties are there other deterrents, like a pause in production or delay a future bid, that would be more effective in mobilizing change? Unions can also push for these violation penalties, and perhaps highlight companies that are doing great work in this space, and those that are not. Incentivize companies to get on the ‘good list’.
There also should be greater emphasis on education, and empowerment, for both employers and employees. Many of these violations can be remedied with correct safety procedures, and an understanding of the serious results that can happen if they’re not followed. This includes being vigilant that basic safety equipment is available at all times, including essential items like a retractable lanyard, fall protection harness, fall arrest harness, rolling ladder, and self-retracting lifeline just to name a few. Scheduling more meetings that include staff, managers, and executives is a great bulwark against safety issues. Beyond team building, it gives everyone a chance to speak out, raise concerns, and suggest solutions that can proactively improve safety.
Practically, we all should improve the safety standards being implemented both on and off-site. That means:
- Providing a wider range of PPE that fits all shapes and sizes, including women; even those who require maternity gear, like the US Army and other military branches are outfitting.
- Improving recordkeeping with modern software, not old-fashioned paper/filing cabinet methods.
- Employers conducting regular inspections, rather than waiting for an OSHA rep to show up.
- Staying on top of the very latest regulations and changes, not adhering to outdated rules that are no longer cutting it.
- Put a greater emphasis on “exercising discretion.” This, in particular, means OSHA refrains from grouping violations when there is evidence of separate and distinct incidents. This leads to more penalties, and more reason to put some businesses in the crosshairs.
- More training. We cannot assume everyone on site knows – or remembers – everything.
These are just some of the ways we can all help OSHA, and each other, to maintain the best possible safety standards; and most importantly, keep people out of harm’s way. The finalized 2023 list from OSHA will be available sometime in the spring of 2024. Look out for it. Make it a priority to ensure you’re in compliance with every standard. Be proactive. Lives literally depend on it.
The information contained in this article is for informational, educational, and promotional purposes only and is based on information available as of the initial date of publication. It is the reader’s responsibility to ensure compliance with all applicable laws, rules, codes and regulations. If there is any question or doubt in regard to any element contained in this article, please consult a licensed professional. Under no circumstances will Global Industrial® be liable for any loss or damage caused by your reliance on this article.